Comprehensive Guide to Laser Engraving Materials
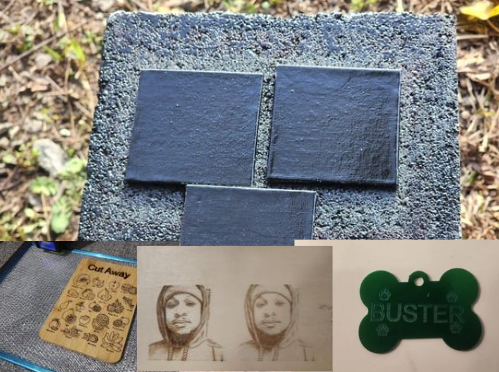
Comprehensive Guide to Laser Engraving Materials
When I think about laser engraving, I know it’s crucial to understand how different materials react with the beam. Each type, whether it's plastic, different types of metals, or for wooden signage, has its own quirks. I’ll dive into what factors you should consider when choosing materials for your engravings, plus some essential safety measures to keep in mind while you work. Come on, let's learn together.
How Laser Engraving Interacts With Various Materials
When you decide to start using your engraver as a laser cutter, you will see how different materials respond to your laser. For instance, metals are stronger than wood or plastics and can withstand high temperatures, which makes it a solid choice for really detailed engravings in different types of manufacturing.
On the flip side, plastics are more delicate and can melt or warp easily if the settings aren’t just right.
Quick secret, maybe not a secret but simply a tip, some metals will also warp or get deformed when you use your laser engraver on them. This is usually because of the thickness and temperature tolerance of the metal. Let's go into the different types of materials and what's needed to engrave or cut them.
Wood and other Organic Materials
When laser engraving wood and organic materials, my main focus is to know the exact type of wood. From bamboo to maple, each has its own engraving techniques or settings per se. Preparing the surface properly is the main key as I have come to find out with all the tests i've done.
When engraving wood, you will need a good way to manage any residue or smoke that comes up during the process.
- Eastern White Pine - 380 lbf
- Yellow Poplar - 540 lbf
- Alder - 590 lbf
- Douglas Fir - 660 lbf
- Southern Yellow Pine - 870 lbf
- Eastern Red Cedar - 900 lbf
- Paper Birch - 910 lbf
- Cherry - 995 lbf
- Black Walnut - 1,010 lbf
- Teak - 1,155 lbf
- Heart Pine - 1,225 lbf
- Yellow Birch - 1,260 lbf
- Red Oak - 1,290 lbf
- American Beech - 1,300 lbf
- Ash - 1,320 lbf
- White Oak - 1,360 lbf
- Hard/Sugar Maple - 1,450 lbf
- Hickory - 1,820 lbf
- Mesquite - 2,345 lbf
- Cocobolo - 2,960 lbf
- Ipe - 3,684 lbf
All this information is from Waterlox.com. Be sure to visit them if you want more information on the hardness of different species of wood.
Here is also a quote from them:
In general, many people would consider wood species that are softer than red oak (1,290 lbf) to be on the softer side and anything red oak or harder would be considered a harder wood. Many people will also classify hardwoods as anything from trees that lose their leaves in the fall (deciduous trees) and soft woods from conifers or evergreens (think pine and fir). This isn’t 100% black and white, but it is usually true.
Let me show you what I have learned about engraving on wood.
Best Practices for Engraving Various Wood Types
The first thing you will want to do ds to focus on surface preparation. A smooth surface helps achieve cleaner and sharper engravings. For example, when I am working with softer woods like say for instance Hickory, I keep my laser settings moderate because they burn easily, which can lead to charring if I am not careful.
Another best practice I've found useful is adjusting the speed and power settings based on the wood type. Hardwoods like or oak require slower speeds and lower power to get the right depth without damaging the surface. This is achieved by making multiple lower power passes instead of one high power pass. Best results will always come from practice and a materials test from Software such as Lightburn.
Guess what I Have for you? Another tip. However, this time it's going to be about a tip I learned for laser cutting wood. If you have an air assist with your laser engraver/cutter, you will get less charring when you're doing your project. However, if you don't have an air assist like I didn't when I first started, you will need to know this simple trick to not getting laser charring on your pieces of wood. It's simple, you just need to put something like craft paper tape over the surface of the piece of wood you're cutting.
Here’s a quick recap of my go-to steps for engraving various wood types:
- Always sand the wood surface before engraving.
- Adjust settings based on whether the wood is soft or hard.
- Monitor the process to prevent charring, especially on softer woods.
Here is a rundown of some of the settings you can try out with your laser engraver. Some of these settings might be off a little as I mainly ran only a couple tests and based some of the other results on knowing the hardness level of the wood. For instance. If i ran Cocobolo at 75% power, speed of 700 mm/min and at 2 passes. Then I would try to run Alder at something like 40% to 50% at 1400 mm/min and run only one pass as this material is way softer than Cocobolo.
- Ipe
Power: 80%
Speed: 600 mm/min
Passes: 2
- Cocobolo
Power: 75%
Speed: 700 mm/min
Passes: 2
- Mesquite
Power: 70%
Speed: 800 mm/min
Passes: 2
- Hickory
Power: 65%
Speed: 900 mm/min
Passes: 1
- Hard/Sugar Maple
Power: 60%
Speed: 1000 mm/min
Passes: 1
- White Oak
Power: 60%
Speed: 1000 mm/min
Passes: 1
- Ash
Power: 60%
Speed: 1000 mm/min
Passes: 1
- American Beech
Power: 60%
Speed: 1000 mm/min
Passes: 1
- Red Oak
Power: 55%
Speed: 1100 mm/min
Passes: 1
- Yellow Birch
Power: 55%
Speed: 1100 mm/min
Passes: 1
- Heart Pine
Power: 55%
Speed: 1100 mm/min
Passes: 1
- Teak
Power: 50%
Speed: 1200 mm/min
Passes: 1
- Black Walnut
Power: 50%
Speed: 1200 mm/min
Passes: 1
- Cherry
Power: 50%
Speed: 1200 mm/min
Passes: 1
- Paper Birch
Power: 45%
Speed: 1300 mm/min
Passes: 1
- Eastern Red Cedar
Power: 45%
Speed: 1300 mm/min
Passes: 1
- Southern Yellow Pine
Power: 45%
Speed: 1300 mm/min
Passes: 1
- Douglas Fir
Power: 40%
Speed: 1400 mm/min
Passes: 1
- Alder
Power: 40%
Speed: 1400 mm/min
Passes: 1
- Yellow Poplar
Power: 35%
Speed: 1500 mm/min
Passes: 1
- Eastern White Pine
Power: 35%
Speed: 1500 mm/min
Passes: 1
Managing Residue and Smoke During Wood Engraving
Managing residue and smoke during wood engraving is super important for keeping my workspace clean and ensuring the quality of my projects. You will find that using an effective exhaust system helps clear away smoke. This helps to reduces the chance of buildup that could interfere with the engraving process. This is also important for your health as you do not want to inhale any of the smoke or soot from laser engraving certain materials.
It's always best to start out by working in a well ventilated area. This way, smoke and other impurities can disperse. Keeping the air flowing not only protects our health but also helps keep the engraving details sharp, as smoke can sometimes settle back onto the workpiece and smudge the design. By focusing on these factors, I can ensure that your wood engraving projects turn out beautifully every time.
Engraving doesn’t stop at wood; there’s a whole world of different materials waiting to be explored. Glass, ceramics, and stone bring their own set of challenges and rewards, and you'll find that each offers a unique canvas for your creativity.
Metals Suitable for Laser Engraving
Engraving metal is something that every engraving enthusiast dream of doing correctly. I’ll be discussing how to work with aluminum and anodized aluminum which are perfect for simple designs. I will also go into how you should precious metals like gold and silver. Let's get started.
Techniques
When it comes to engraving stainless steel, you will want to pay attention to adjusting the frequency of the laser for achieving clean results. A higher frequency often works better for detailed designs because it removes less of the metal surface. I remember not really knowing how to explain frequency when it involves laser engraving, but, I got the perfect answer from someone on Reddit. He said "Think of frequency as sandpaper, the higher the number, the finer the details and the less materials will be removed". I think that that's the best way someone can explain it without sounding too nerdy.
Usually if the engraving speed is too slow, it can cause overheating and damage to the material. I've noticed many thinner type of metals will even warp when the laser gets to a certain temperature. On the other hand, if you do it too fast, you might not get the details you want. When you balance speed, power, and frequency, that is when you get your best results. Here are the key takeaways from this section:
- Aluminum and anodized aluminum are ideal for simple designs.
- For precious metals like gold and silver, special care is needed, but they can be engraved beautifully.
- Frequency adjustment is crucial for engraving stainless steel, higher frequencies help with detailed designs by removing less material.
- A helpful analogy for frequency: it's like sandpaper, the higher the number, the finer the details and less material is removed.
- Speed matters - too slow can cause overheating and warping, too fast may miss certain fine details. Balance is key to great results.
Working With Aluminum and Anodized Aluminum
These are some of the best materials that I have worked with. Especially the anodized ones. They are just so easy to engrave as you're only really removing the top layer coating. I’ve found that aluminum is easy to engrave, which makes it a favorite for projects like custom signs and business cards. You can achieve amazing results with machines as simple as diode lasers.
Engraving any of these materials is massively rewarding. One thing to remember when laser engraving anodized aluminum is that the anodization process is usually only done to prevent corrosion. However, sometimes it is done to just add flavor to the piece. This is especially true when it comes to items like business cards.
Engraving Precious Metals Like Gold and Silver
Engraving gold and silver is a unique experience that can bring out extra beauty in these. Using a fiber laser for this process will be your best bet, as it allows for precise etching without causing any damage to the soft surface of these metals. A laser diode can sometimes be used to engrave different types of gold and silver depending on if they have been anodized.
We all probably dream about laser engraving these type of metals, but, we have to remember how expensive these specific materials can be. It's not going too be like pieces of wood that you can mess up and just get another piece to try again on. Gold and silver are usually engraved because someone wants to do something special for themself or someone else. This is where the cost to engrave these materials will differ from other types of materials.
Here are some steps you can follow when engraving precious metals:
- Choose a fiber laser for detailed etching or engraving.
- Consider using a laser diode for a softer touch especially when the precious metal has been anodized.
- Adjust laser settings carefully for optimal results.
Types of laser engravers and their pros and cons
Diode Lasers
Diode lasers are some of the cheapest laser engravers
Pros:
- Compact size
- Energy-efficient
- Low maintenance
- Cost-effective
- Versatility with softer materials
Cons:
- Limited power
- Lower precision
- Limited material compatibility
CO2 Lasers
Pros:
- High power
- Excellent for non-metals
- Great engraving detail
- Relatively affordable
Cons:
Lower efficiency
Requires regular maintenance
Limited to thinner metals
Larger footprint
Fiber Lasers
Pros:
- High power and speed
- Precision
- Low maintenance
- Energy efficiency
Cons:
Higher cost
Limited use on non-metals
Less versatility
One popular fiber laser engraver on the market is the
Conclusion
Understanding the compatibility of various materials for laser engraving is crucial for achieving high-quality results. Each material, whether it's metal, plastic, wood, or fabric, has specific characteristics that influence the engraving process, so recognizing these differences can save time and reduce mistakes. Following safety measures and adjusting settings based on material types also plays a vital role in maintaining a safe workspace and ensuring a successful project.
Related Articles
-
How to Laser Engrave Leather | Step-By-Step Guide
Can You Laser Engrave Leather?
How to Laser Engrave White Tiles Painted Black?
What Is The Best Low Cost Laser Engraver? My Opinion
How to Laser Engrave Acrylic with a Diode Laser: A Step-by-Step Guide
My Hands-On Review of the Monport 6-Watt Diode Laser Engraver
Laser Etching Glass
Laser Engraving A Photo | Full Guide
How Much Does Laser Engraving Cost
Is Laser Engraving Hard to Learn?
Why is laser engraving so expensive?
WHAT IS A LASER CUTTING MACHINE?
Top 7 Laser Engraving Business Ideas
10 Essential Safety Precautions for Home Laser Engraving Projects
Laser Engraving Cutting Boards | How To
Where To Buy Laser Cutting Materials?
Laser Engraving QR Codes
What Is DPI In Laser Engraving
How Much Is A Laser Engraving Machine